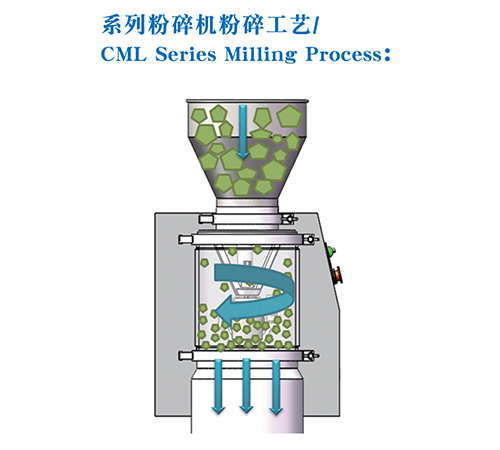
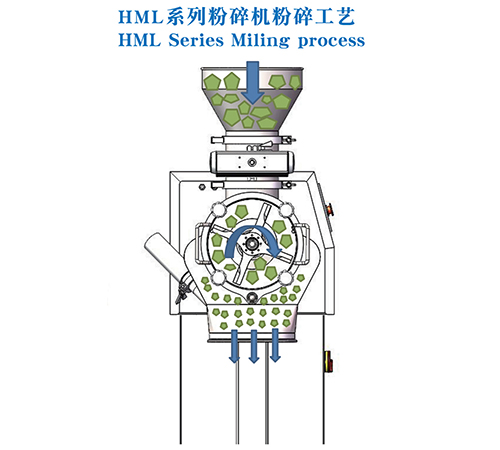
Kartion jyrsintä
Kartiomyllyjä tai kartiomaisia seulamyllyjä on perinteisesti käytetty vähentämään farmaseuttisten aineosien kokoa yhtenäisellä tavalla. Niitä voidaan kuitenkin käyttää myös sekoittamiseen, seulomiseen ja dispergoimiseen. Niitä on erikokoisia, mukaan lukien pöytälaboratoriolaitteet täysimittaisiin, suuritehoisiin koneisiin, joita käytetään suuriin lääkekäsittelytoimintoihin.
Vaikka kartiomyllyjen käyttötarkoitukset vaihtelevat, suuntaus käyttää niitä lääkkeissä sisältää kuivattujen materiaalien paakkujen poistamisen tuotannon aikana; kosteiden granuloitujen hiukkasten mitoitus ennen kuivaamista; ja kuivarakeistettujen hiukkasten liimaus niiden kuivaamisen jälkeen ja ennen tabletointia.
Muihin jyrsintätekniikoihin verrattuna kartiomylly tarjoaa myös muita erityisiä etuja lääkevalmistajille. Näitä etuja ovat alhaisempi melu, tasaisempi hiukkaskoko, suunnittelun joustavuus ja suurempi kapasiteetti.
Markkinoiden innovatiivisin jyrsintätekniikka tarjoaa paremman suorituskyvyn ja tuotteen kokojakauman. Lisäksi niitä on saatavana vaihtelevalla seulalla (siivilä) ja juoksupyörällä. Kun seulaa käytetään pienitiheyksisten materiaalien kanssa, se voi lisätä tehoa yli 50 prosenttia verrattuna myllyihin, jotka on suunniteltu suorilla tankoilla. Joissakin tapauksissa käyttäjät ovat saavuttaneet yksikkötuotantokapasiteetin jopa 3 tonnia tunnissa.
Pölyttömän kartiojyrsinnän saavuttaminen
On tunnettua, että jyrsinnässä syntyy pölyä, joka voi olla erityisen vaarallista käyttäjille ja lääketeollisuuden ympäristölle, jos pölyä ei ole suljettu. On olemassa useita menetelmiä pölyn eristämiseen.
Bin-to-bin-jyrsintä on täysin in-line-prosessi, joka perustuu painovoimaan syöttääkseen ainekset kartiomyllyn läpi. Teknikot sijoittavat säiliön myllyn alle, ja suoraan tehtaan yläpuolelle sijoitettu siilo vapauttaa materiaalit tehtaalle. Painovoima mahdollistaa materiaalin kulkemisen suoraan pohjasäiliöön jyrsinnän jälkeen. Tämä pitää tuotteen sisällä alusta loppuun ja helpottaa materiaalin siirtoa jälkijyrsinnän jälkeen.
Toinen menetelmä on tyhjiösiirto, joka on myös in-line-prosessi. Tämä prosessi sisältää pölyä ja myös automatisoitua prosessia auttaakseen asiakkaita saavuttamaan korkeamman tehokkuuden ja kustannussäästöjä. In-line-tyhjiönsiirtojärjestelmän avulla teknikot voivat syöttää materiaalia kartion kourun läpi ja vetää ne automaattisesti tehtaan ulostuloaukosta. Siten prosessi alusta loppuun on täysin suljettu.
Lopuksi suositellaan isolaattorijauhatusta, joka sisältää hienojakoisia jauheita jauhamisen aikana. Tällä menetelmällä kartiomylly integroituu isolaattoriin seinäkiinnityslaipan kautta. Kartiomyllyn laippa ja konfiguraatio mahdollistavat kartiomyllyn pään fyysisen jakamisen eristimen ulkopuolella olevalla käsittelyalueella. Tämä kokoonpano mahdollistaa minkä tahansa puhdistuksen suorittamisen isolaattorin sisällä hansikaslokeron avulla. Tämä vähentää pölyaltistuksen riskiä ja estää pölyn siirtymisen käsittelylinjan muille alueille.
Vasarajyrsintä
Vasaramyllyt, joita jotkut lääketeollisuuden valmistajat kutsuvat myös turbomyllyiksi, soveltuvat tyypillisesti tutkimukseen ja tuotekehitykseen sekä jatkuvaan tai erätuotantoon. Niitä käytetään usein tapauksissa, joissa lääkekehittäjät vaativat vaikeasti jauhattavien API:iden ja muiden aineiden tarkkoja hiukkasten vähentämistä. Lisäksi vasaramyllyillä voidaan ottaa talteen rikkoutuneita tabletteja jauhamalla ne jauheeksi reformointia varten.
Esimerkiksi tarkastuksessa jotkin valmistetut tabletit eivät välttämättä ole asiakkaan standardien mukaisia useista syistä: väärän kovuuden, huonon ulkonäön sekä yli- tai alipainon vuoksi. Tällaisissa tapauksissa valmistaja voi halutessaan jauhaa tabletit takaisin jauhemaiseen muotoonsa sen sijaan, että he menettäisivät materiaalit. Tablettien jauhaminen uudelleen ja tuotantoon ottaminen vähentää viime kädessä hukkaa ja lisää tuottavuutta. Lähes kaikissa tilanteissa, joissa tabletti-erä ei täytä vaatimuksia, valmistajat voivat käyttää vasaramyllyä ongelman ratkaisemiseksi.
Vasaramyllyt pystyvät toimimaan nopeuksilla 1 000 rpm - 6 000 rpm ja tuottavat jopa 1 500 kiloa tunnissa. Tämän saavuttamiseksi jotkut myllyt on varustettu automaattisella pyörivällä venttiilillä, jonka avulla teknikot voivat täyttää jauhatuskammion tasaisesti aineilla ilman ylitäyttöä. Ylitäytön estämisen lisäksi tällaiset automaattiset syöttölaitteet voivat ohjata jauheen virtausta jauhatuskammioon prosessin toistettavuuden lisäämiseksi ja lämmön muodostumisen vähentämiseksi.
Joissakin edistyneemmissä vasaramyllyissä on kaksipuolinen teräkokoonpano, joka lisää märkien tai kuivien ainesosien käyttökelpoisuutta. Terän toinen puoli toimii vasarana, joka murskaa kuivat materiaalit, kun taas veitsen kaltainen puoli voi viipaloida märät ainekset. Käyttäjät yksinkertaisesti kääntävät roottoria jauhettavien ainesosien perusteella. Lisäksi jotkin myllyn roottorikokoonpanot voidaan kääntää, jotta ne voidaan säätää tietyn tuotteen käyttäytymisen mukaan, kun myllyn kierto pysyy muuttumattomana.
Joissakin vasaramyllyissä hiukkaskoko määritetään myllylle valitun seulakoon perusteella. Nykyaikaiset vasaramyllyt voivat pienentää materiaalin koon niin pieneksi kuin 0,2–3 mm. Kun käsittely on valmis, mylly työntää hiukkaset seulan läpi, mikä säätelee tuotteen kokoa. Terä ja seula toimivat yhdessä lopullisen tuotteen koon määrittämiseksi.
Postitusaika: 8.8.2022